The jaw crusher is a coarse crushing device used mainly for the crushing of stones and ores, such as river pebbles, pebbles, and granite. The jaw crusher * appeared in 1858. It was * widely used in road construction and later applied to mines. It is now available for medium-sized crushing of various ores and bulk materials. The highest compressive strength of the fractured material is 320 MPa. The jaw crusher also has the characteristics of large crushing rate, uniform product size, simple structure, reliable operation, simple maintenance and low operating cost.
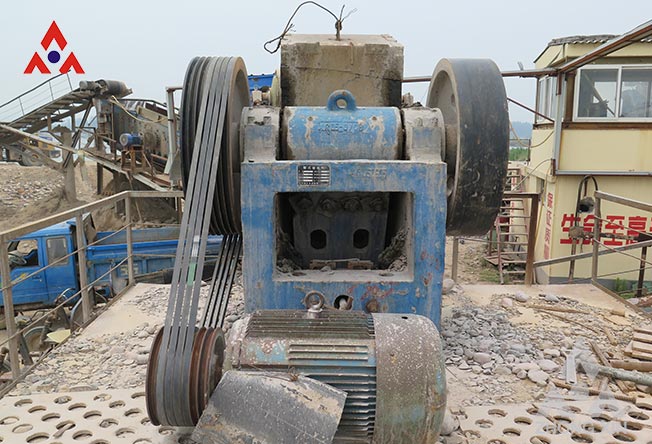
When the jaw crusher is in operation, the motor is used as power. The eccentric shaft is driven by the V-belt and the pulley through the motor pulley, so that the movable cymbal reciprocates according to the predetermined trajectory and enters the fixed cymbal, the movable cymbal and the side guard. The material in the crushing chamber composed of the plates is broken, and the finished material is discharged through the lower discharge port. The discharge port (discharge port) can be adjusted according to the needs of the user to obtain a qualified product material size. The different materials purchased by the customer, the different materials and the broken particles of the crusher are also different. So how to adjust the discharge granularity?
1. Adjust the size of the particles by adjusting the tension spring and adjusting the rear wedge to adjust the two wedges between the rear seat of the thrust plate and the frame. This method is suitable for small crushers.
2. Adjust the washer by placing a set of washers between the rear of the support base of the rear thrust plate and the rear wall of the frame. The purpose of adjusting the discharge port can be achieved by increasing or decreasing the number of gaskets or changing the thickness.